- Yancheng Xiangsheng Carbon Fiber Technology Co., LTD. Chopped carbon fiber: Micro reinforcing unit for high-performance materials!
- The demand scale of the domestic carbon fiber industry!
- In July, with high temperatures and busy work schedules, Yancheng Xiangsheng Carbon Fiber Technology Co., Ltd. shows its advantages in short-cut carbon fiber!
- The market size and growth of the carbon fiber industry!
- Congratulations: Hu Lijie, the general manager of Yancheng Xiangsheng Carbon Fiber Technology Co., LTD., has become a member of the China Chemical Writers Association!
- Congratulations: Hu Lijie, the general manager of Yancheng Xiangsheng Carbon Fiber Technology Co., LTD., has had his series of poems "Man in the Mist" selected for print publication and joined the documentary of the China Poetry Society!
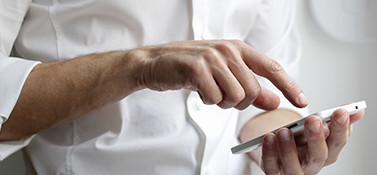
- Contact:Mr. Hu
- Cellphone:0086 - 18021868999
- Telphone:0086 - 0515-82230000
- Email:826955488@qq.com
- Address:No.1, Tonggang Road, science and Technology Park, Haitong Town, Sheyang County, Yancheng City, Jiangsu Province
Yesterday, we spoke with experts from the UK's TWI. We explored the idea of replacing traditional metal materials with carbon fiber composite materials, especially in making important structural components. There are too many factors to be considered to determine priorities. Make a list today of the design points for the structural components of a carbon fiber composite.
The composite structure of the content is generally referred to as the structure of carbon fiber preleaching.
Strength and rigidity
Since it is a structural component, the designer must first consider strength and rigidity. The component has the ability to resist deformation and destruction under the action of external force loading, but there is a limit to this ability.
How to determine the load of the parts, the capability limit of the components is not exceeded, which is calculated through the mechanical calculation of materials. The limit of the component's capacity is the question that the structural designer of the carbon fiber composite material needs to consider.
Through the reasonable collocation fiber and resin, optimize the fiber layout, use the least materials, meet the design requirements, reflect the composite material designer's exquisite technique. However, the factors that determine the strength and stiffness of composite materials are not only related to the type of fiber and resin, but also to the orientation of carbon fiber and the combination of layers and layers.
Therefore, when designing the structural components of carbon fiber composite materials, the designers should consider the mechanical properties of the three hierarchical structures.
Composed of matrix and reinforcing materials compound single-layer material, its mechanical performance is determined by the composition of material mechanical properties, phase geometry () each phase materials, shape, distribution, content and interface area of the performance.
The mechanical properties of the layers are determined by the mechanical properties and layering geometry of the single-layer materials (the thickness, the laying direction and the layering sequence).
The top-level structure refers to the engineering structure or product structure commonly referred to, and its mechanical properties are determined by the mechanical properties and structural geometry of the composite.
The stability of
In addition to the requirements of strength and stiffness, the designers of the composite material parts instability, especially for some thin rod structure, when pressure, should be able to ensure its original linear equilibrium state. For some frame structure components, if the layer is not uniform, the warp instability can also be produced, so pay special attention to the manufacturing process. It is best to use a symmetrical layer to prevent uneven deformation.
In general, it is not allowed to produce instability when the component is not reaching the ultimate load. However, if there are some special requirements that can produce instability, the design process will not affect the ultimate load during the design process.
Layer structure
The laying structure is the key of the structural design of carbon fiber composite materials. How to transfer the excellent performance of the single-layer structure to the composite structure parts, the laying structure plays an important role. The following points should be paid attention to:
1. Resin is a short plate for the mechanical properties of carbon fiber composite materials, so try to avoid adding the load directly to the interlayer or resin. In other words, 0 °, plus or minus 45 °, 90 ° fiber should have, or load parts from no fibre arrangement direction will be torn apart.
2. In order to avoid the cracks of the laminated plate, it is not more than 5 storeys to avoid repeating a single direction.
3. In order to prevent the outermost layer of the peel, in parts of the main direction of the load, should be laying plus or minus 45 ° fiber, not laying 0 ° and 90 ° fiber. In addition, avoid the outer layer of layoff or incomplete.
4. If the asymmetric layer is used, each layer will appear warping due to the different thermal expansion coefficient of the same side. Therefore, the symmetrical layer should be used generally.
5. When adding the reinforcing layer, the minimum number of stairs should be 3.8-6.4 mm, and the additional layer should be used as the symmetrical layer.
concatenon
In the development of the components of carbon fiber composite materials, it is not possible to adopt the whole molding technique, and the connection between the parts and parts is required, and the connection form is designed.
Generally speaking, there are three forms of connection of carbon fiber composite components: mechanical connection, cementing connection and mixed connection. The mechanical connection is suitable for large thickness, high reliability and high concentration load. Cementing is mainly used to connect the parts to an integral whole.
Mixed connection is a combination of cementing and mechanical connection. It can improve the performance of anti-stripping, impact resistance, fatigue resistance and creep resistance.
Fatigue and impact damage
Compared with metal materials, the fatigue of composite materials must be considered for temperature, humidity and impact damage. In most cases, impact injuries cover fatigue problems in structural design.
fatigue
In general, the tensile fatigue of composite materials is superior to that of metal. The cracking relative stability of fatigue or alternating loading under the action of orthogonal laminates is slower than that of metal cracking. It is necessary to pay attention to the compression, shear and interlayer shear of the composite material under the action of alternating load. The early damage caused by fatigue is as follows:
1. Notch, sharp Angle
2. Cross section mutation
3. The protrusions
Extreme eccentric loading
5. Bolt connection joint
6. Quick wobble
Impact damage
For the structure of carbon fiber composite materials, CAI intensity (post-impact compression strength) should be considered as one of the design parameters. That's the way the plane determines damage tolerance. Damage tolerance is the allowable damage range in the component. If this limit is exceeded, the damage will significantly affect the performance of the component. The impact damage tolerance of carbon fiber composite materials must be considered as one of the design parameters within the detectable range.
Even if there is invisible damage to the naked eye, it is important to ensure that the structure does not decrease the CAI intensity. The damage tolerance of shock damage can be improved by adding aramid fibers or fiberglass to carbon fiber materials.
- Yancheng Xiangsheng Carbon Fiber Technology Co., LTD. Chopped carbon fiber: Micro reinforc
- The demand scale of the domestic carbon fiber industry!
- In July, with high temperatures and busy work schedules, Yancheng Xiangsheng Carbon Fiber
- The market size and growth of the carbon fiber industry!
- Congratulations: Hu Lijie, the general manager of Yancheng Xiangsheng Carbon Fiber Technol
- Congratulations: Hu Lijie, the general manager of Yancheng Xiangsheng Carbon Fiber Technol