- Carbon fiber Industry in 2025: Market Expansion from Aerospace to New Energy Vehicles!
- Yancheng Xiangsheng Carbon Fiber: Specialized in short-cutting technology, leading the way in quality carbon fiber!
- Forecast of the Future Development Trend of the Carbon Fiber Industry!
- The summer solstice has passed. Yancheng Xiangsheng Carbon Fiber Technology Co., Ltd. showcases the outstanding performance and diverse applications of its chopped carbon fibers!
- On the summer solstice, explore the mystery of short-cut carbon fiber at Yancheng Xiangsheng Carbon Fiber Technology Co., LTD.!
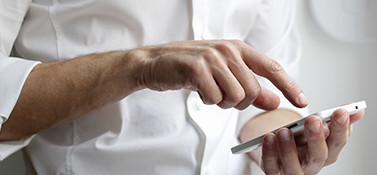
- Contact:Mr. Hu
- Cellphone:0086 - 18021868999
- Telphone:0086 - 0515-82230000
- Email:826955488@qq.com
- Address:No.1, Tonggang Road, science and Technology Park, Haitong Town, Sheyang County, Yancheng City, Jiangsu Province
Drilling Process of Carbon Fiber Composites
Release date: [2016/11/24]
Read total of [1065] times
Carbon Fiber Composite (CFRP) is widely used in the fields of aerospace, defense and military, automobile and aircraft components because of its excellent properties such as high strength, high modulus, low density, high temperature resistance, corrosion resistance, abrasion resistance and fatigue resistance. The Airbus A380, for example, has been used in about 32 tons of carbon fiber composites, accounting for 15% of the total, and other types of composites are estimated to be about 25% of the total weight. Drilling is the most common carbon fiber composite materials, one of the secondary processing methods, the hole is mainly used for riveting or fastening structural parts. However, because of its anisotropy and inhomogeneity, low strength of interlayer bonding and large temperature influence, carbon fiber composites are prone to defects such as delamination, burr and tearing during drilling hole making. Typical hard-to-machine materials.
The results show that the layered defects have the greatest influence on the load-bearing capacity and fatigue strength of the composite structures. Keywords: carbon fiber composites; In this paper, the current research status of carbon fiber composite drilling in China is reviewed from the aspects of mechanism, influencing factors and detection of delamination defects in carbon fiber composite drilling process.
Mechanism Analysis of
Due to the particularity of CFRP mechanical properties and the diversity of internal structure, the deformation process of the material is much more complex than the metal material in the cutting process, which is not only related to the traditional factors such as tool shape and process parameters, but also by fiber and matrix properties As well as the direct effect of the direction of fiber laying. Therefore, CFRP cutting mechanism and the traditional metal-cutting processing mechanism is very different.
1.CFRP cutting mechanism
In 1983, Koplev et al earlier experimental study of carbon fiber cutting process, pointed out that the CFRP chip is mainly formed by the brittle fracture of the material. D.H. Wang et al. Investigated the effects of different fiber orientations on the formation mechanism of the chip by orthogonal cutting experiments on unidirectional and multidirectional carbon fiber composites. Because the carbon fiber composite material is composed of brittle carbon fiber and tough resin matrix, the strength limit of the two is very different, the former is several times of the latter, so the scholar Zhang Houjiang and so on that in the cutting process can be simplified as just carbon fiber , While the cutting of the resin matrix will be neglected.
\
Fig.1 Cutting process under different fiber direction angle θ
In this paper, some typical fiber ply directions are studied, and the formation of chips under different fiber orientation angles θ (see Fig. 1) is summarized.
When θ = 0 °, the formation of the chip is the tool by continuously cutting layer material and the base material separated from the realization. This cutting deformation is called interlayer separation.
When 0 ° <θ ≤ 90 °, in Figure 1 θ = 45 ° and θ = 90 ° as the representative of the tool cutting edge of the carbon fiber composite material to push the formation of fibers within the fiber perpendicular to the axis of its own shear stress . When the shear stress exceeds the fiber shear strength limit, the fiber is cut. The cut fiber slips along the fiber direction under the pushing action of the tool rake face. When the shearing stress between the fiber interfaces caused by the slip exceeds the shearing strength limit of the matrix resin material, the cut fibers are separated from the other fibers to form chips. This cutting deformation is called a fiber cutting type.
When 90 ° <θ <180 °, in Figure 1, θ = 45 ° as the representative of the tool to push the front end of the role of material led to the interlayer separation between composite materials. The tool tip material bending under the action of the tool, when the bending stress exceeds the bending strength of carbon fiber composite material limit, the bottom fracture. Tool to move forward, the tool on the front end of the material to enhance the role of push, when the end of the material at the bottom of the fracture point of shear stress exceeds the material shear strength limit, the occurrence of shear fracture, the formation of chips. This form of cutting deformation is called bending shear type.
The results show that the layered defects have the greatest influence on the load-bearing capacity and fatigue strength of the composite structures. Keywords: carbon fiber composites; In this paper, the current research status of carbon fiber composite drilling in China is reviewed from the aspects of mechanism, influencing factors and detection of delamination defects in carbon fiber composite drilling process.
Mechanism Analysis of
Due to the particularity of CFRP mechanical properties and the diversity of internal structure, the deformation process of the material is much more complex than the metal material in the cutting process, which is not only related to the traditional factors such as tool shape and process parameters, but also by fiber and matrix properties As well as the direct effect of the direction of fiber laying. Therefore, CFRP cutting mechanism and the traditional metal-cutting processing mechanism is very different.
1.CFRP cutting mechanism
In 1983, Koplev et al earlier experimental study of carbon fiber cutting process, pointed out that the CFRP chip is mainly formed by the brittle fracture of the material. D.H. Wang et al. Investigated the effects of different fiber orientations on the formation mechanism of the chip by orthogonal cutting experiments on unidirectional and multidirectional carbon fiber composites. Because the carbon fiber composite material is composed of brittle carbon fiber and tough resin matrix, the strength limit of the two is very different, the former is several times of the latter, so the scholar Zhang Houjiang and so on that in the cutting process can be simplified as just carbon fiber , While the cutting of the resin matrix will be neglected.
\
Fig.1 Cutting process under different fiber direction angle θ
In this paper, some typical fiber ply directions are studied, and the formation of chips under different fiber orientation angles θ (see Fig. 1) is summarized.
When θ = 0 °, the formation of the chip is the tool by continuously cutting layer material and the base material separated from the realization. This cutting deformation is called interlayer separation.
When 0 ° <θ ≤ 90 °, in Figure 1 θ = 45 ° and θ = 90 ° as the representative of the tool cutting edge of the carbon fiber composite material to push the formation of fibers within the fiber perpendicular to the axis of its own shear stress . When the shear stress exceeds the fiber shear strength limit, the fiber is cut. The cut fiber slips along the fiber direction under the pushing action of the tool rake face. When the shearing stress between the fiber interfaces caused by the slip exceeds the shearing strength limit of the matrix resin material, the cut fibers are separated from the other fibers to form chips. This cutting deformation is called a fiber cutting type.
When 90 ° <θ <180 °, in Figure 1, θ = 45 ° as the representative of the tool to push the front end of the role of material led to the interlayer separation between composite materials. The tool tip material bending under the action of the tool, when the bending stress exceeds the bending strength of carbon fiber composite material limit, the bottom fracture. Tool to move forward, the tool on the front end of the material to enhance the role of push, when the end of the material at the bottom of the fracture point of shear stress exceeds the material shear strength limit, the occurrence of shear fracture, the formation of chips. This form of cutting deformation is called bending shear type.
Lastest News
- Yancheng Xiangsheng Carbon Fiber: Specialized in short-cutting technology, leading the way
- Carbon fiber Industry in 2025: Market Expansion from Aerospace to New Energy Vehicles!
- The summer solstice has passed. Yancheng Xiangsheng Carbon Fiber Technology Co., Ltd. show
- Forecast of the Future Development Trend of the Carbon Fiber Industry!
- On the summer solstice, explore the mystery of short-cut carbon fiber at Yancheng Xiangshe
- Yancheng Xiangsheng Carbon Fiber Technology Co., LTD. Chopped Carbon Fiber: The Key to Inn